概述

六家行业领导者(nTopology、Ansys、EOS、Stress Engineering Services、North Star Imaging 和Synopsys)接受高难度挑战,利用各自公司的先进技术,开发了一套创新设计换热器的解决方案。
该项目旨在提升换热器能效和系统性能的同时,使用更少材料,占用更小空间。并将设计、模拟、CT 检测、试验结合起来,有利于对这款新颖的高成本产品进行质量控制。最终的模型设计实现了减少零件、降低压降、增加传热的预期。
亮点
- 为改善体积受限应用中的性能而重新设计换热器
- 首次尝试即可成功打印部件
- 运用扫描、检测和模拟技术比较设计件和制造件的性能
- 零破坏的完整 NDE 检测
- 实物测试验证传热和强度分析
设计过程
大多数新型换热器的应用都受到空间限制,随着热量的增加要求更小的空间和更高效设计。然而,在常见的换热器设计中创新相对较少,一般是低效的管壳式几何结构。通过采用隐式几何结构,换热器复杂的曲面设计可以使其在性能方面有显著地提高。
该项目见证了 nTopology 和 Ansys 合作生成和模拟换热器的创新型设计。nTopology 使用隐式几何技术创建三周期极小曲面(TPMS),因其平滑的拓扑结构在流体动力学中对换热器非常有利。此外,TPMS设计隔离了两个区域(热和冷),并且具有较高的强度重量比,使它们成为轻量化的理想选择。

对于重新设计,nTopology 定义了一个填充 TPMS 几何结构的换热器,实现了将零件数量从 40 减少到只有一个,总重减少了 81%。创建多个不同的设计方案,在 Ansys 软件中测试。先使用 Ansys Discovery Live 在不同的设计迭代中进行实时的流体流动模拟,再用 Ansys Fluent CFD 仿真对比传统换热器设计和TPMS 换热器的性能。研究结果令人印象深刻,体积减少 85%,单位体积传热增长 11.7 倍,单位质量传热增加 9.4 倍。

Ansys 利用仿真工具从设计上优化构建过程,评估了如最佳取向、自定义的支撑结构设计和其他输入等因素,从而帮助降低对打印效果的风险,并最大限度地缩短构建时间。Ansys 软件中的工艺仿真也有助于预测变形、孔隙率和微观结构,以及所选 EOS M290 打印机的特定工艺参数等因素。

关于制造,EOS 在设置打印之前做了些进一步的预处理,包括远程监控以确保没有任何问题发生。第一次尝试就获得了不错的 3D 打印成品,两个耗时约 62 小时,然后执行包含热处理在内的后处理步骤,创建一个高质量的 3D 打印部件。
CT 扫描和基于图像的检测
该部分由 North Star Imaging 进行 CT 扫描创建图像数据集,然后导入 Simpleware 软件比较设计件和制造件的性能。采用 Simpleware 软件对 CT 数据进行分割,识别固体和流体区域,通过对孔隙、孔洞和裂纹的目视检查进行缺陷检测。然后建立固体和流体区域的面模型(STL文件),将其与设计件的 STL 文件叠加进行表面偏差分析。借助这种方法,可以直接识别出因制造工艺过程产生与设计之间的差异。
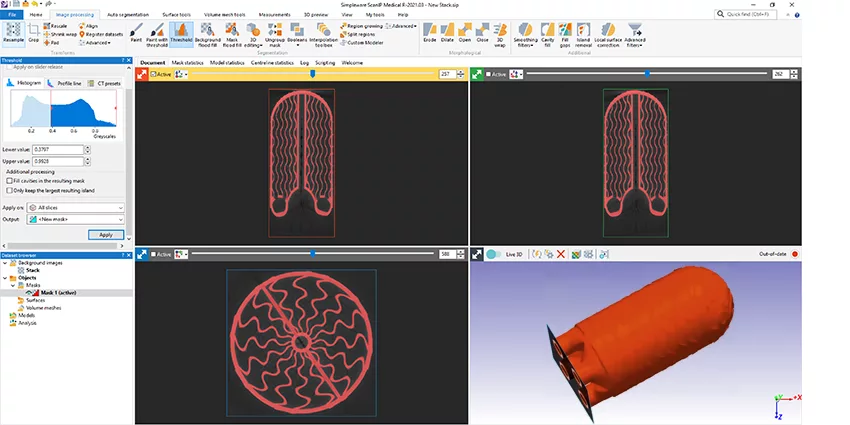
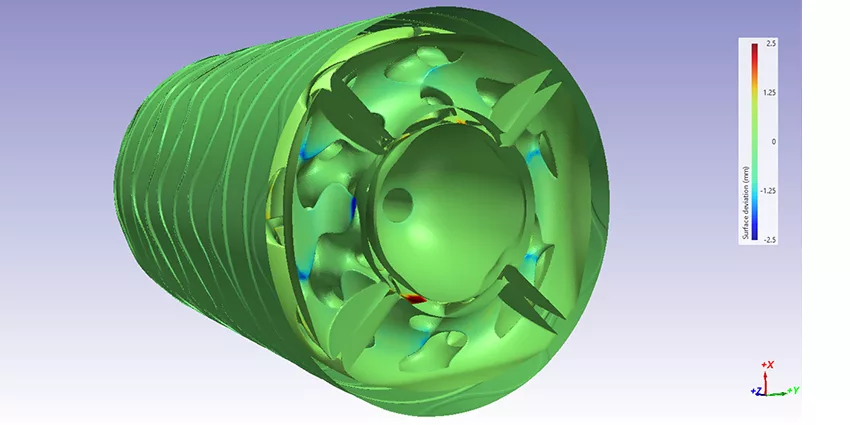
就换热器而言,两个模型之间的偏差很小,由于打印的方式在换热器底部的一些小区域产生了倒圆和过量粉末。但总的来说,打印成品非常贴近原始拓扑设计。这种基于图像的工作流程还可以利用机器学习实现自动化,快速完成导入、分割、提供用户所需的关键测量数据,降低因操作人员不同而产生差异的风险。
FE 网格划分和模拟
工作流程的下一步是查看设计件与制造件的性能对比。在Simpleware 软件中生成多区域有限元网格,导出专用于 Ansys 软件的模型格式。

然后在 Ansys 中对模型进行大变形塑性分析,验证爆破压力。基于 Ansys 的增材制造材料库赋予材质属性,对比由 nTopology 扫描获得的网格与原始 CAD 网格。创建网格的子模型,在无需耗费大量计算资源的情况下进一步分析换热器性能。
根据模拟结果显示,制造件和设计件的性能非常相似。相较于前一版变形略有改善,可能是局部增厚的结果。为增强对换热器性能的信心,Stress Engineering Services 进行了一系列的实物物理试验,包括环境暴露和冲击振动、传热和压降等。与其他换热器相比,TPMS 设计的性能明显更好,特别是在流量方面。而且,TPMS 模型超过了大于 14 倍 350 psi 的爆破压力要求,表明其适用于实际应用。
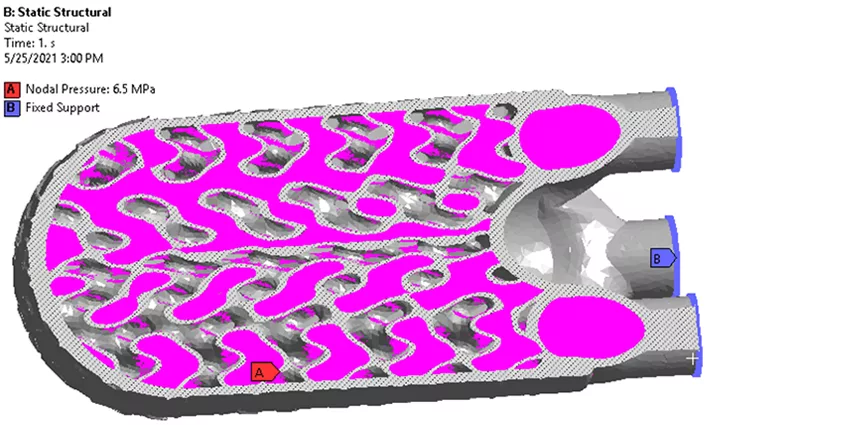
实物试验
然后将该制造件安装到 Stress Engineering Services 的实物流动传热测试装置,测量压降和总传热系数。通过向换热器传输冷液、热液测试换热器的性能。试验过程中采用热成像可视化换热器内的热量分布。热液温度随热液或冷夜流量相关函数变化的试验结果表明,热液温度随流量增大而降低,在冷夜流量约 1 GPM 和热液 50 华氏度左右,温度变化最大。并比较 3D 打印换热器与传统商用的现有黄铜管壳式换热器的性能。
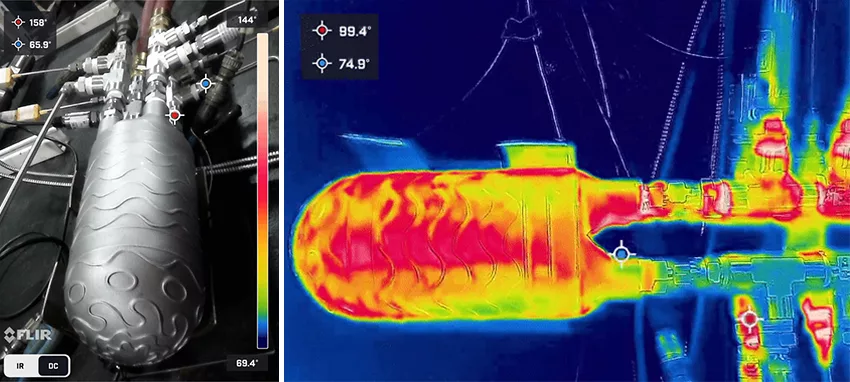
流动传热测试之后,再对换热器进行压力测试。在各个阶段逐渐增加压力直至失效(失压)。在压力测试期间,采用精密的数字图像相关法(DIC)系统测量换热器的变形。DIC 系统使用光学成像测量表面位移、计算应变。与应变计类似,但可以测量试样件的整个可见表面。然后将测试的应变与有限元分析比较,改进分析模型。
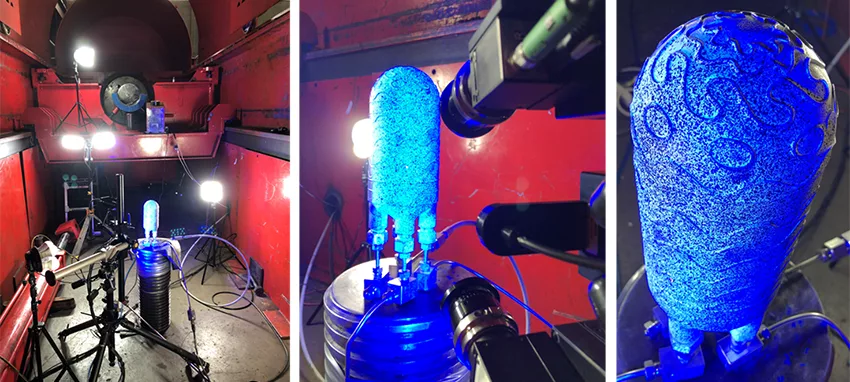
爆破试验后的 CT 扫描
为建立验证工作流程,对经过爆破试验的换热器原型再次扫描成像,可视化失效发生的区域。在换热器底座附近形成裂纹的 4 个区域与爆破试验中检测到的失效位置相对应。换热器原型的性能已远超预期,但如果有提升到更高级别性能的需求,这种试验后的成像和可视化能够帮助识别待重新审视和强化设计的区域。
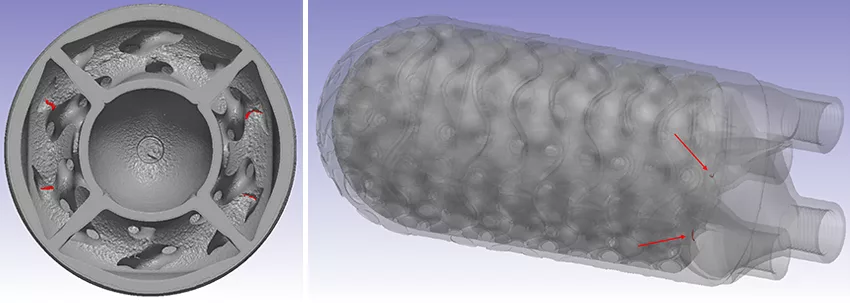
结果和结论
采用 TPMS 重新设计的换热器非常成功地改善了性能,同时因考虑空间限制问题还减小了尺寸。与传统设计相比,TPMS 部件实现显著改进,体积减少 85 %,总重降低 81 %,单位体积传热增加 11.7 倍,单位质量传热增加 9.4 倍,单位体积表面积增加 7.9 倍。此外,TPMS 设计使高温侧压降减少 9.1 倍,低温侧压降增加 1.16 倍。将原本由 40 个或更多零件构成的换热器简化为一个部件,也是代表该项目成功的一个亮点。
通过这个工作流程,每个参与的合作伙伴都演示了如何将最新的设计、检测、增材制造和模拟技术相结合,助力重新设计和验证关键组件的性能。该方法在降低材料成本、加速设计到部件的过程、提高多个领域的效率方面都有着巨大的潜力。
参考
- 观看“先进制造之旅”系列的 6 个讲座视频,提供包含设计、模拟、制造、测试和质量控制的完整工作流程:https://www.synopsys.com/simpleware/news-and-events/advanced-manufacturing.html