概述
当材料在任意荷载作用下出现应力引起的新裂纹时,材料的应力状态会发生显著变化,应力的重分布将导致脆性岩石材料中原有裂纹发生扩展、钝化或改向,对材料的强度产生影响。由于循环加载和疲劳效应,在较小荷载作用下脆性材料就可能发生破坏,这种破坏属于材料的“疲劳”破坏。地铁隧道边墙、大坝、巷道顶板、桥梁和路基等在循环/重复荷载作用下均可能发生劣化。
损伤力学研究一般关注水平和竖直变形/应变,而这些变形是微/纳裂纹形成和扩展的结果。本研究结合试验与扫描电子显微镜(SEM)、计算机层析成像(CT)技术对断裂过程区(FPZ)进行观察和分析,探索断裂韧度(KIC)与循环载荷的关系。
试验和模拟
按照 ISRM 标准开展巴西圆盘试验和断裂韧度试验,在静力和重复加载测试下均重复 5 次。用于巴西圆盘试验的岩石试样为凝灰岩。岩石试样的单轴抗压强度(UCS)为 123 MPa,巴西圆盘试样直径为 51 mm。V 型切槽巴西圆盘(CCNBD)试样中存在切槽裂纹,适用于各种断裂型加载。

开展采用径向间接拉伸应力的重复加载试验,正弦加载试验中荷载频率为 1 Hz。正弦循环加载试验从约 2/3 材料抗拉强度的高应力水平开始,然后将施加荷载降低约 10% 直到试样在较低应力水平下不再断裂,此时的应力水平称为试样的疲劳极限。
数值模拟中的非均质性采用扩展有限元法(XFEM)和 Simpleware 软件实现。将 CT 图像数据导入 Simpleware 软件进行图像处理,量化测试样本中 FPZ 的微断裂体积/面积,生成高质量的网格模型用于 ABAQUS 软件中的数值模拟。
结果与讨论
在线弹性断裂力学(LEFM)理论中,裂纹尖端应力情况可由3 种常见的断裂状态表征,对应为 I 型(拉伸应力)、II 型(剪切应力)和III 型(撕裂应力)裂纹扩展模式。材料的断裂模式属于上述哪种取决于裂纹几何形态及表面位移。I 型断裂条件下,由裂纹尖端开始,裂纹表面预计产生一个开口;II 型断裂条件下,裂纹面产生面内滑移;III 型断裂条件下,由于裂纹面外剪切作用,裂纹面垂直于裂纹轴线移动。
拉伸强度和断裂韧度
取 5 个试样测试结果的平均值,得到静态巴西拉伸强度为 11 MPa,静态 I 型(拉伸)断裂韧度为 1.48 MPa·m1/2。巴西圆盘试样和 CCNBD 试样在重复荷载作用下均成功完成疲劳试验。S-N 曲线显示,CCNBD 试样强度随荷载幅值的增加而降低,极限韧性强度由于疲劳冲击降低了 35%(1.48 kN 至 1.21 kN),KIC 降低至 30%。结果表明,当裂纹尖端的 KI 低于单一加载下确定的 KIC 时,裂纹可能发生扩展。这一结果与经典断裂力学理论相矛盾,经典断裂力学认为,只要 KI 低于 KIC,裂纹就不可能扩展。



疲劳裂纹
试样疲劳裂纹的张开和闭合同步记录中,脆性岩石在发生小的塑性变形后突然破坏,试验过程中记录了试样破坏之前裂纹像弹性弹簧一样张合。以往研究表明,裂纹的形成和破坏是一个单调的过程。而本研究中数小时的观测结果记录了宏观疲劳裂纹在试样没有最终破坏前发生张合,与许多断裂理论以及脆性材料的力学行为不一致。


应力-CMOD 循环曲线
CCNBD 和巴西试样的应力-CMOD(裂纹口的开口位移)循环曲线图中可观察到高塑性变形的形成,变形的累积表明在裂纹尖端形成了 FPZ(如图 a)。图 b和图 c 显示沿 x 和 y 方向的位移,从这种大量不致破坏的塑性变形可推测出试样中产生了疲劳损伤。随损伤的增加,径向轴位移和 CMOD 以不同速率增加。CMOD 起始于较小的弹性变形,随后发生快速塑性变形并累积。在重复加载的巴西试验中,拉应力引起的疲劳开裂则是非常有趣的破坏行为。随着 CMOD 值(正值)的增加,中心疲劳裂纹开始张开。CMOD 读数描述了由试验中 60% 累积塑性变形导致的裂纹张开。当CMOD 读数由正值变为负值时,表明疲劳裂纹开始闭合。塑性变形的累积随着裂纹闭合而持续发生直到最终断裂。
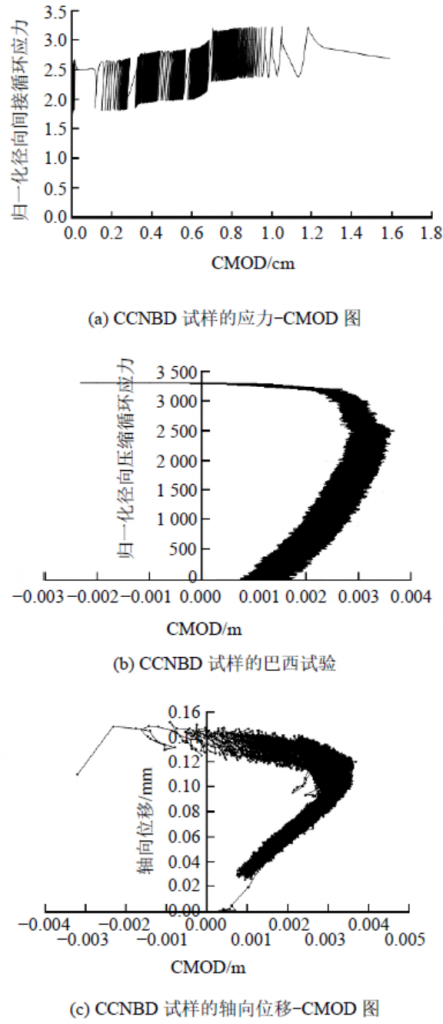
断裂过程区裂纹
利用 CT 扫描确定 FPZ 及切槽裂纹前的微观和宏观裂纹,通过 SEM 分析研究切槽裂纹前的损伤区。宏观裂纹的形成始于切槽裂纹尖端,FPZ 的发展则是切槽裂纹尖端大量能量积聚的结果,新裂纹的形成导致积聚能量的减少。CCNBD 试样在几何形状上具有显著优势,可以直接聚焦和研究裂纹尖端,带有尘埃和小颗粒的破坏面粗糙形貌表明了裂纹尖端 FPZ 的发展。

本研究认为,晶粒与基体之间产生的局部应力和原始微裂纹导致裂纹尖端前的闭合力向张开力的转变。当 σ1 = σt(σ1 为最大主应力,σt 为最大拉应力)时,

当切槽裂纹倾角为 60º 时得到 FPZmax,表明 I-II 型混合模式时 FPZmax 可发展。SEM 图像和3D 图形中也可以看到 FPZ 内的拉伸和剪切应力以及尘埃和小颗粒的存在。

数值模拟
采用基于 XFEM 程序的数值计算方法研究裂纹尖端的初始应力和断裂特性,分别开展静力加载和重复加载工况计算切槽裂纹处及其周围的疲劳效应。在静载作用下,CCNBD 试样切槽裂纹尖端的能量积聚低于循环加载情况。循环加载作用下形成了更多裂纹和小颗粒,使得荷载所做的功更多。此外,积聚的能量从裂纹尖端向外逐渐释放。

重复加载作用下,拉应力的分布发生在切槽裂纹前,形成一个宽的 FPZ。而在静载作用下,仅沿切槽裂纹轴线而非尖端存在拉伸影响区域。

已有研究阐明岩石疲劳的特征,即与静力加载相比,FPZ 中存在更多微小和亚临界裂纹,这一结果与本文试验和数值模拟结果一致。图 a、b 为单一加载和重复加载作用下破坏面的实际差异。在重复加载作用下,确定了 CCNBD 试样裂纹尖端处具有细小颗粒和尘埃的损伤区域(图 b)。而在静力加载下破坏的 CCNBD 试样中,裂纹尖端前几乎没有尘埃和小颗粒(图 a)。XFEM 数值计算得到了类似的结果(图 c、d)。因此,采用 CCNBD 试样和 V 形裂纹对 FPZ 进行研究,对于探索脆性材料的疲劳机制是必要且有益的。

结论
本研究在静力加载和重复加载作用下进行了断裂韧度和间接巴西拉伸强度试验。由于重复加载,静态 KIC 最大值降低了 35%,间接巴西强度最大值降低了 30%。这两种强度的降低表征着疲劳效应对岩石抗拉强度的影响。
在 CCNBD 和巴西圆盘试样的重复加载试验中,获得裂纹尖端前的永久累积应变,从而量化了 FPZ 中发展的微断裂引起的损伤。CT 和SEM 结果表明,在重复载荷下巴西圆盘和 CCNBD 试样的破坏是由于存在包含许多微小裂纹而非单条宏观裂纹的 FPZ。在循环加载条件下,CCNBD 试样切槽裂纹尖端前有一个包含大量碎屑颗粒的破碎区。而在静载条件下,试样的破坏面没有观察到碎屑颗粒。FPZmax 仅在当切槽裂纹倾角为 60º 时获得。裂纹尖端前闭合力和张开力之间的转变是由于晶粒、基体和已有微裂纹之间产生的局部应力所致。因此,在脆性岩石中,可见疲劳裂纹的张开和闭合表现为弹性行为,不会导致破坏。此外,本研究在岩石力学领域首次使用摄像机记录了数小时的可见疲劳裂纹张合现象。
参考
- ERARSLAN N. Investigation of the fracture process zone and behavior of the macro-scale fatigue cracks in brittle rock specimens[J]. Rock and Soil Mechanics, 2023, 44(7): 4.
- ERARSLAN Nazife.脆性岩石试样断裂过程区及宏观疲劳裂纹行为研究[J].岩土力学, 2023, 44(7):2041-2049.