概述
钢铁产量中近 70% 来自采用高炉(BF)工艺生产的生铁,因此钢的成本很大程度上取决于 BF 的寿命。由于耐火材料的劣化,BF 的寿命有限,特别是聚集着液态金属的高炉炉膛中使用的耐火材料。设计更具有适应性的新型耐火材料需要全面了解工作过程中发生的劣化机制,而各种机制都取决于耐火材料的孔隙结构,并受到多孔介质中传输的限制。
本项目基于 X 射线计算机断层扫描(XCT)获得 3D 孔隙结构,开发并测试了一种耐火材料中熔融金属渗透的演化模型。假设等温渗透,材料中存在的相具有不同的润湿性且碳相选择性溶解,分析不同初始熔融金属成分和各种润湿条件对渗透过程演变的影响。
试样准备
微孔碳材料由 Tokai COBEX 公司生产,主要原料是人造石墨粒、人造半石墨粉、硅粉和氧化铝粉,煤焦油沥青为粘结剂。固体颗粒与粘结剂的比例为3.64:1。将混合原料成型为 2500 × 700 × 500 mm3 的块体,在标准环形炉内还原气氛下烘烤,从制成样品中切割直径和高均为 10 mm的圆柱体作为试样,采用 XCT 进行分析。
准备三种类型的基材用于润湿性测量:石墨(G)、氧化铝(A)和碳化粘结剂(B),全部由用于生产微孔碳材料的相同原材料制备。为获得样品的各种化学成分,准备生铁废料、化学纯铁、工业纯铁、化学纯锰和两个对照熔体,分别表示为:M2C、M3C 和 M4C。为验证化学成分,在每次熔炼后使用 Foundry-Master 光谱仪分析铸铁样品的化学成分。

数据处理
使用 Nanotom 180S 设备(GE)进行 XCT 扫描,将原始图像数据裁剪为 1.25 × 1.25 × 1.25 mm3 的立方体,导入 Simpleware ScanIP 软件进行图像处理。基于灰度值分割为 5 个不同的相:碳化粘结剂(棕色)、石墨(蓝色)、氧化铝(绿色)、开孔(红色)和闭孔(黄色),其中使用 Flood Fill 3D 算法工具识别开孔。

在 Simpleware FE 模块采用 +FE Free 算法创建高质量的体积网格。设置参数:目标最小长度 16.68 µm;目标最大误差 0.42 µm;最大边长 41.67 µm;表面变化率 100;内部变化率 30;单个边界层厚度 4.17 µm。生成的网格模型由超过 450 万个四面体单元组成,在计算中仅使用代表连续孔隙结构的 3D 网格(503287 个单元)。为整个体积创建 3D 网格以便于选择代表开孔结构和其他相(即碳化粘结剂、石墨和氧化铝)之间的边界,以 Nastran 格式(*.nas 文件)导出网格模型用于 COMSOL Multiphysics 软件中的模拟。
使用高温光学显微镜 EM201(Hesse)进行润湿性分析,测量用试样为规则的圆柱体(直径和高均为 3 mm)。每种类型的基材(石墨、碳化粘结剂和氧化铝)均使用三种金属成分(M2C、M3C 和 M4C)进行测试。
孔隙尺度流动模拟
多相耐火材料的渗透演化模型与碳相的选择性溶解相结合,基于以下假设:
- 熔融金属的流动发生在由 XCT 扫描获得微孔碳材料开孔结构的 3D 几何形状中。整个结构内先是空气,逐渐充满熔融金属。渗透在等温条件(1550℃)下进行,驱动力是压力梯度。
- 由于几何形状复杂,特征长度非常小,压力梯度低,熔融金属动态粘度高,雷诺数非常小(接近0)。因此,使用 Stokes 方程对金属的流动进行建模。
- 该模型假设碳相以不同的速率选择性溶解,具体取决于与熔融金属接触的相。因此,将 Stokes 方程和水平集方法与质量平衡方程耦合。
结果
初始碳浓度对润湿性的影响
该模型的一组输入参数是所研究体积中存在相(即石墨、碳化粘结剂和氧化铝)的初始接触角,取达到 1550℃ 后前十次测量(50 s)的平均值。随熔融金属中碳浓度的增加,氧化铝和碳化粘结剂的接触角略有增加。对于石墨,M2C 和 M3C 的初始接触角相似,碳浓度增至 M4C 时降低。

数值模拟的体积选择
在分割过程中,使用 3D Flood Fill 工具算法识别开孔结构。体素尺寸为 4.167 × 4.167 × 4.167 µm3,在高炉中生铁无法渗透小于 5 µm 的孔隙。因此,对于金属渗透过程的建模,这些孔是无法进入的,因此可被认为是闭孔。
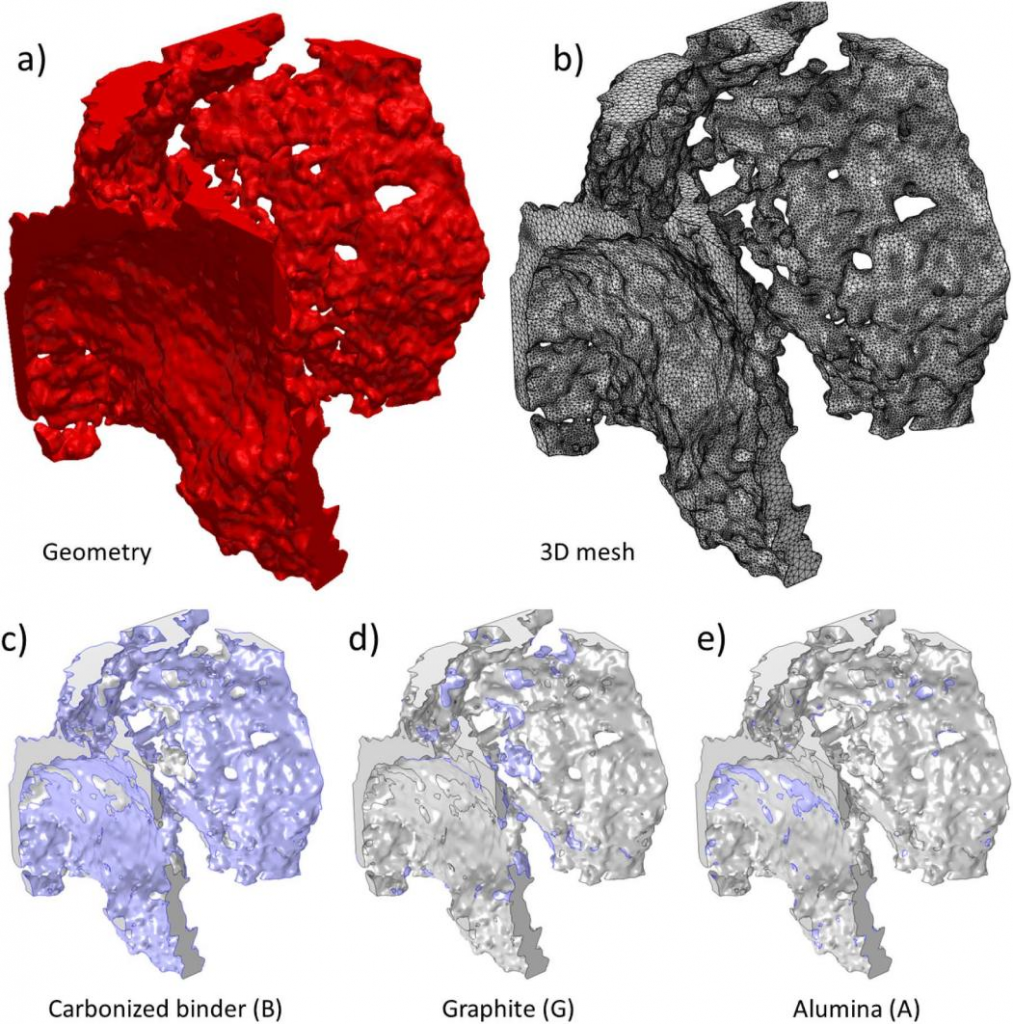
碳化粘结剂是与开孔结构接触的主要相,因此它主要控制渗透过程的演变。粘结剂表面碳化量(88.52%)远高于固体颗粒与粘结剂之间的比例(3.64:1)。然而,大且细长的孔隙在材料整个体积中的分布并不均匀。计算域是从分析的体积中选择,需要包含所有耐火材料相,同时要调整其大小以便适用于当前的计算能力。

熔融金属渗透演化的建模
在含 2 wt% 碳(M2C)熔融金属对耐火碳材料渗透 0.1 s 的模拟中,速度场分布显示(i)速度场乘以水平集函数(彩色),呈现渗透前缘位置的变化;(ii)速度矢量(红色箭头)。由于采用两相流方法,矢量表示两相(金属和空气)的速度,展示了流动路径。5·10-4 s 后,熔融金属到达出口边界。
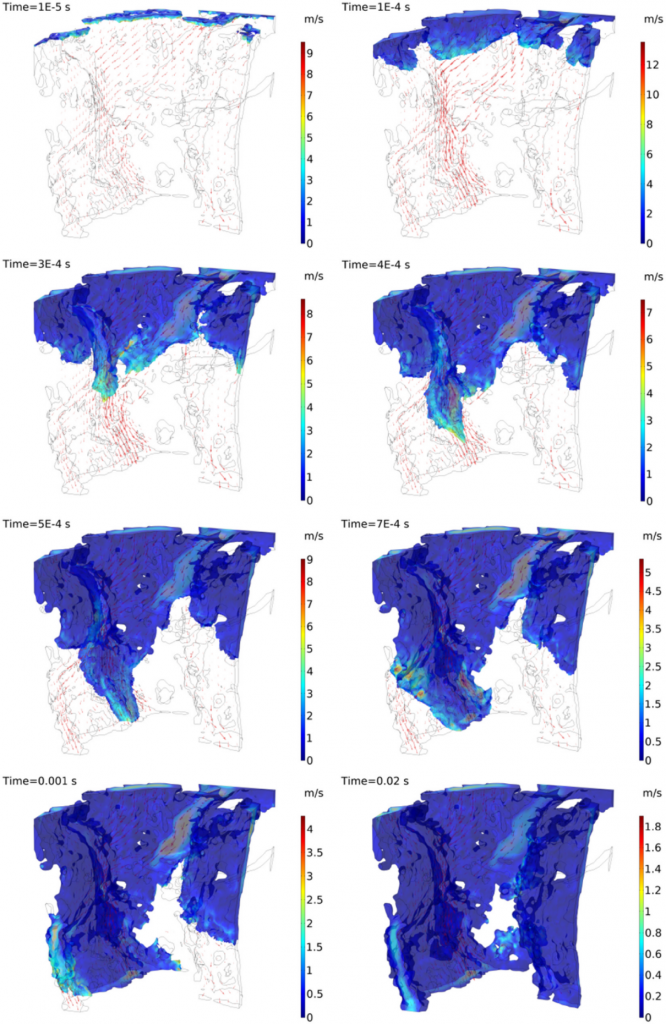
整个体积内的碳浓度分布中,由于空气的碳浓度为 0,故在渗透前缘也呈现出变化。在渗透的初始阶段(低于 0.001 s),主要变化是熔融金属流动的结果,浓度值接近 2 wt%。在孔隙边界处选定的小区域中,即使渗透时间非常短(如 3·10-4 s),碳浓度也开始增加。局部富集位于熔融金属与石墨接触的区域,其溶解速率比碳化粘结剂高一个数量级。填充整个体积后,大多数区域都可以观察到碳溶解。
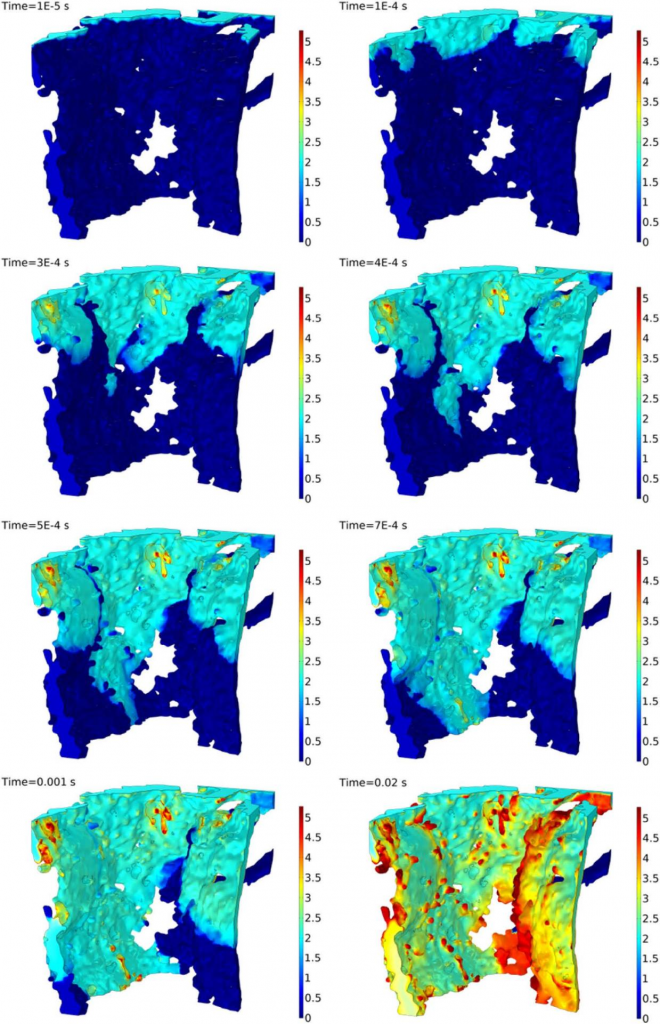
为定量描述渗透过程,引入三个参数:熔融金属的总出口通量(JM)、饱和度参数(βS)和平均碳浓度(cAν)。渗透过程在 10-5 s 后开始,在 10-3 s 达到 90% 饱和度。在约 70% 饱和度时,JM 开始呈指数增加,达到最大值后又减小至 0.42 g/s 的恒定值。在通量达到稳定水平后饱和度略有增加,表明不必填充整个孔隙结构即可接收恒定的总熔融金属通量。cAν 和 βS 的对比显示,填充过程比碳浓度增加得更快。
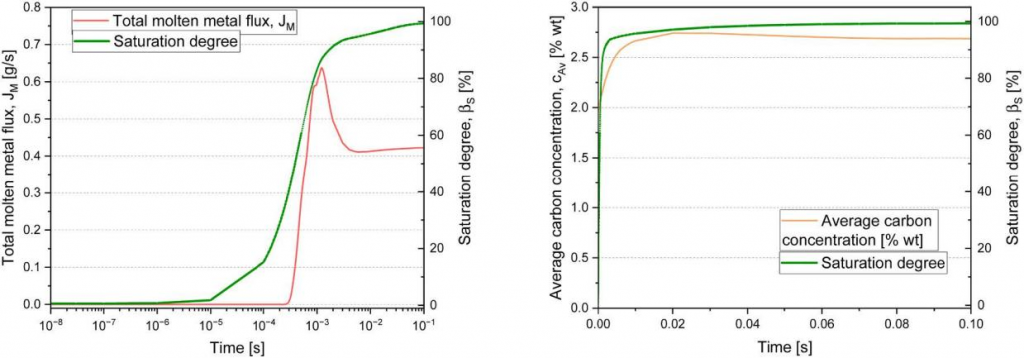
初始碳饱和度的影响
使用精细模型分析初始碳浓度对渗透过程演变的影响。在选定渗透时间的速度场中,渗透前缘的位置都非常相似。
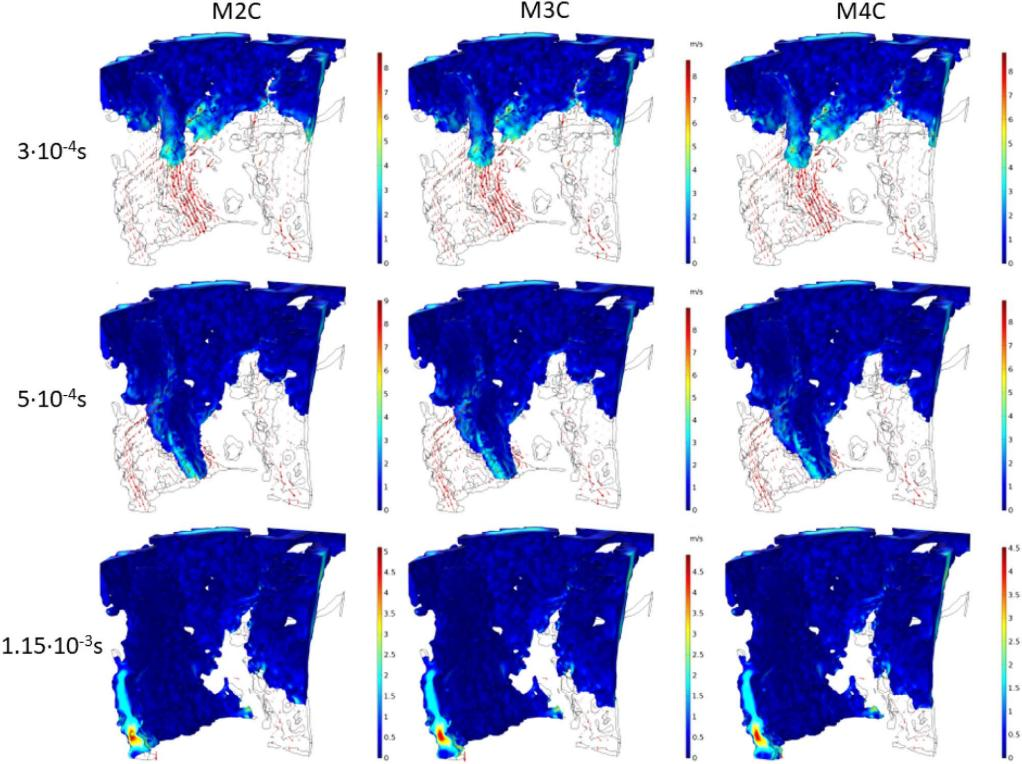
最大总出口通量在较高初始碳浓度下出现最早,且随初始碳浓度的增加而增大。在达到最大值后,均降低到相同水平。对于所有金属成分来说,饱和度 βS 随渗透时间的变化几乎相同。
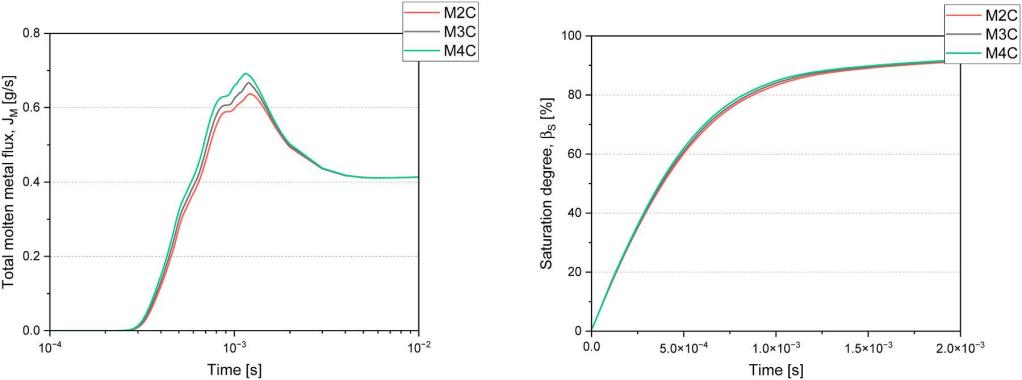
平均碳浓度的增加与初始碳浓度成反比。虽然初始碳浓度对渗透前缘的演变没有很大影响,但对碳相的选择性溶解进而对耐火材料的劣化具有更显著的影响。
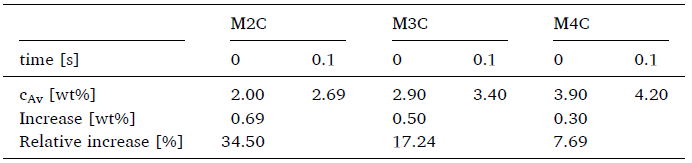
润湿性的影响
由于与开孔接触的耐火材料表面 88% 以上是碳化粘结剂,它的润湿性则主要决定了渗透过程的演变。为定量描述接触角值的影响,假设整个开孔仅接触石墨、碳化粘结剂和氧化铝中的一种,分别对 M2C 进行模拟。t = 4·10-4 s 时,碳化粘结剂的渗透前缘与供参考的微孔碳材料非常相似,氧化铝已到达了出口边界,而石墨的渗透则浅得多。
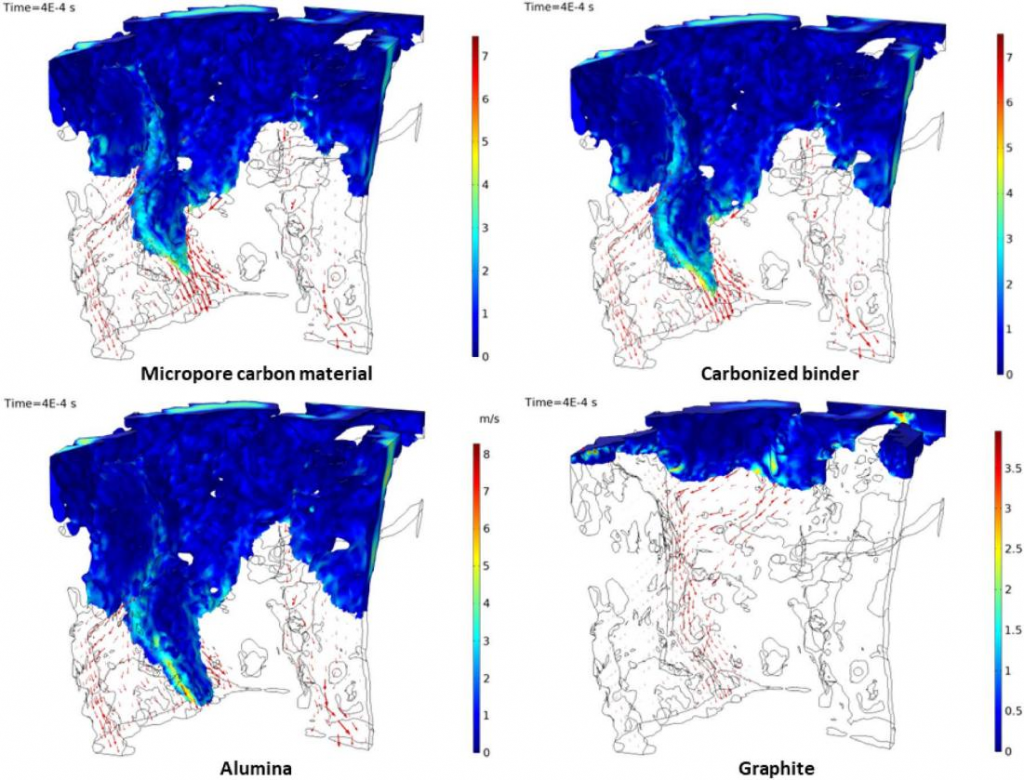
在较短的渗透时间下观察到氧化铝具有最大出口通量,粘结剂与微孔碳材料相似。各种材料的饱和度随时间变化也相似,差异性略高于不同初始碳浓度的影响。石墨和其他三种体系的主要区别在于前者是润湿的,而后者不被熔融金属润湿。
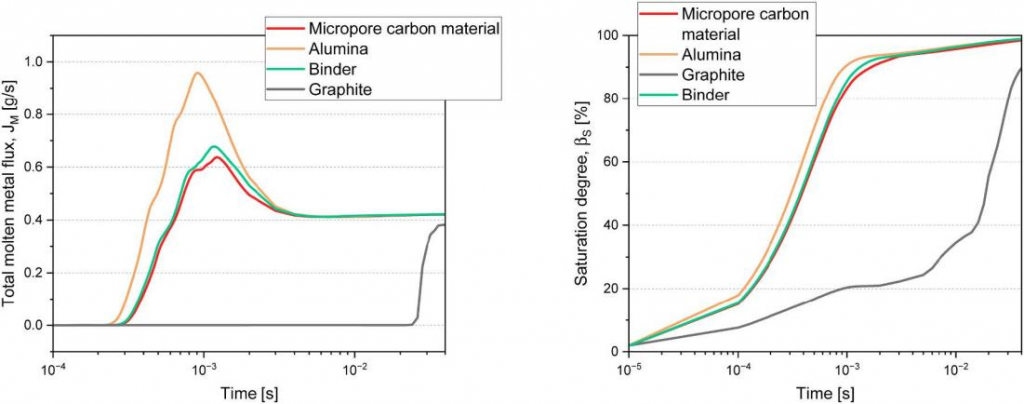
结论
本项目提出通过 XCT 获得微孔碳材料 3D 孔隙结构中碳相选择性溶解的熔融金属渗透模型,分析初始碳浓度和润湿条件对渗透过程演变的影响。
- 在渗透的初始阶段,碳溶解是局部的,即在石墨颗粒表面上观察到。随着时间的推移,碳化粘结剂表面也观察到碳浓度的增加,特别是在熔融金属速度较低的区域。
- 初始碳浓度轻微影响渗透前缘的演变和饱和度。熔融金属的成分可能对选择性溶解产生强烈影响,从而显著影响耐火材料的整体劣化,由此产生的微观结构变化也可能改变渗透前缘的演变。
- 耐火材料的特性、孔表面与熔融金属之间的接触角比熔融金属中碳的初始浓度对渗透前缘的演变具有更显著的影响。通过适当设计材料的微观结构(如将润湿的颗粒放置在非润湿基体表面)能够延迟渗透过程。
参考
- Stec J, Tarasiuk J, Wroński S, et al. Influence of wettability and initial metal composition on infiltration process of carbon refractory material: The evolutional model of molten metal infiltration into a 3D real microstructure acquired using X-ray computed tomography[J]. Journal of the European Ceramic Society, 2024, 44(4): 2662-2676.