概述
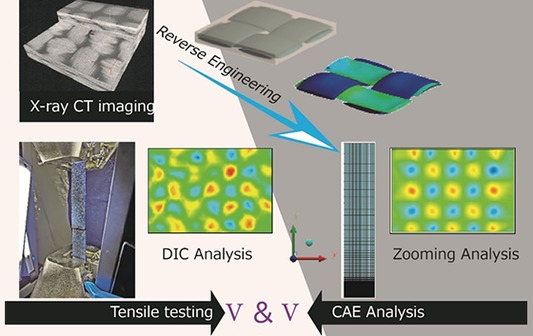
由于复合材料的复杂结构和材料特性,碳纤维增强材料的测试通常比较困难。为解决这个问题,岛津公司(Shimadzu)和 Cybernet Systems 的研究人员开发了一个可以比较 CAE 分析与织物材料真实测量的工作流程。
本案例研究展示了 CAE 分析的工作流程,采用微焦X射线 CT 系统扫描碳纤维增强热塑性(CFRTP)织物材料,获得其内部结构。将扫描结构导入 Simpleware 软件重建后进行多尺度分析和微观尺度的断裂行为模拟。测试系统的实测与 CAE 多尺度分析结果的比较可论证该技术的价值。
亮点
- 使用 Synopsys 公司的 Simpleware 软件重建复杂复合材料的内部结构。
- 利用 CAE 工具进行多尺度分析模拟,Sim™ 工具有助于加深对材料性能的研究。
- 该方法有助于行业内结合测量和分析技术,从而更高效地进行材料和产品设计
介绍
用于运输的碳纤维增强材料和其他复合材料可以设计为减重和环保的复合材料。但复合材料内部结构的复杂性和材料性能的各向异性导致测试会比较困难,需要一种实际测量与仿真相结合的产品设计方法应对这一挑战,这对具有复杂材料性能和变形行为的纤维增强复合材料尤为重要。
为了解决这个问题,研究人员开发了一个包含 Simpleware 软件作为其中一环的 CAE 分析工作流程,比较CAE 分析与实际测量的结果。采用微焦 X 射线 CT 系统扫描碳纤维增强热塑性(CFRTP)织物材料获取内部结构,然后进行多尺度分析,模拟微观尺度的断裂行为。将测试系统的实测结果与 CAE 多尺度分析结果进行对比,论证该技术的价值。
微观结构的生成
为利用均质化技术预测材料的物理性能参数值,需要提供用于分析模型的微观结构形态作为已知量。使用 Ansys®的 Multiscale.SimTM 插件基于微观结构的形态参数生成模型,对默认的结构数据(模型1)和采用微焦 X 射线 CT 系统(inspeXio™ SMX™-225CT FPD HR, Shimadzu)扫描的 CFRTP 织物材料生成的结构数据(模型2)进行虚拟材料测试/数值材料测试(NMT)。
将图像数据导入 Simpleware 软件中识别纤维束的横截面形状、间距和体积分数,然后利用 Ansys CAE 软件和 Multiscale.Sim 进行虚拟材料试验,对一个单元格在不同变形模式和其他条件下从每个方向的应力-应变特性获得三个方向的各向异性弹性模量。另外,通过对矩形试样模型的电算分析估量微观尺度的应变分布。
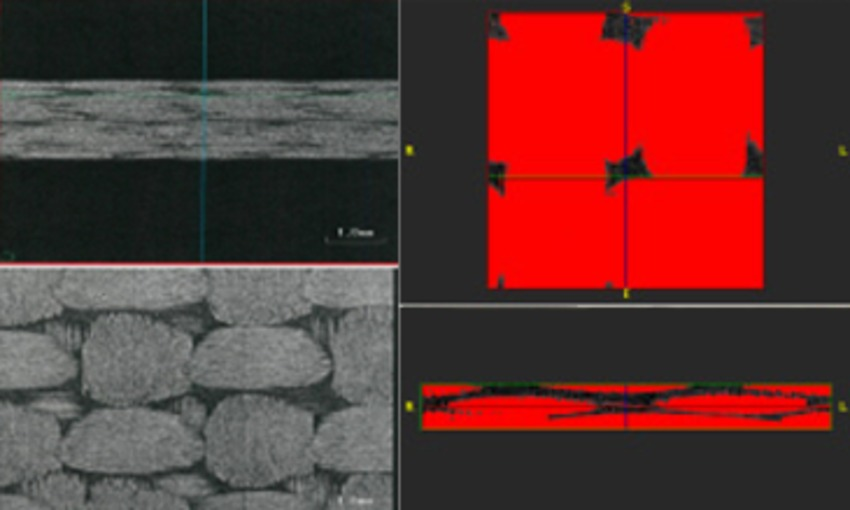
获取实际测量数据
利用精密万能试验机(AGXTM – V,岛津公司)和非接触式数字视频引伸计(TRViewX(SP.1.0.0),岛津公司)从试样中获取与加载同步的单轴拉伸试验(实际测量)图像数据。通过应力应变关系得到试样的纵向弹性模量(杨氏模量),利用数字图像相关(DIC)技术获得试样表面的应变分布。
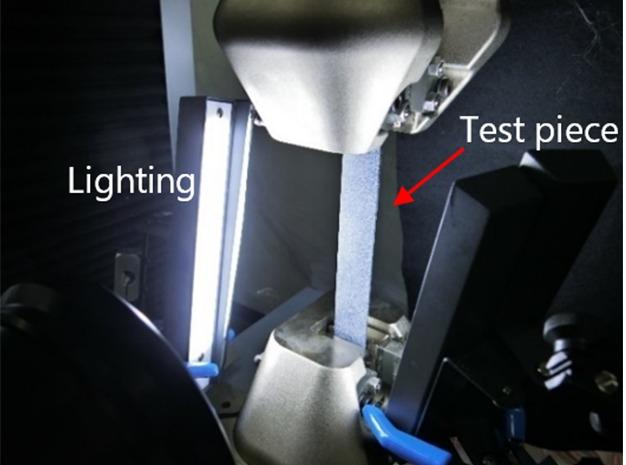
为识别材料受限,通过在虚拟空间中排列拍摄的CT图像展示任意需要的截面图像,获取试验试样的 MPR(Multi Planar Reconstruction)图像。这种方法使得观察碳纤维的排列和界面变得容易。
比较CAE和实际测量值
采用默认结构数据和图像数据建立的两种模型进行仿真,后者显示出非均匀纤维束。对通过 CAE/NMT 和单轴拉伸试验(实测)确定的弹性模量进行比较,单轴拉伸试验获得的弹性模量为 55.46(GPa),而默认结构数据的是 32.56(GPa),表现出较大的误差。相比之下,模型 2 的结果为 51.75(GPa),因此与实测值更接近。
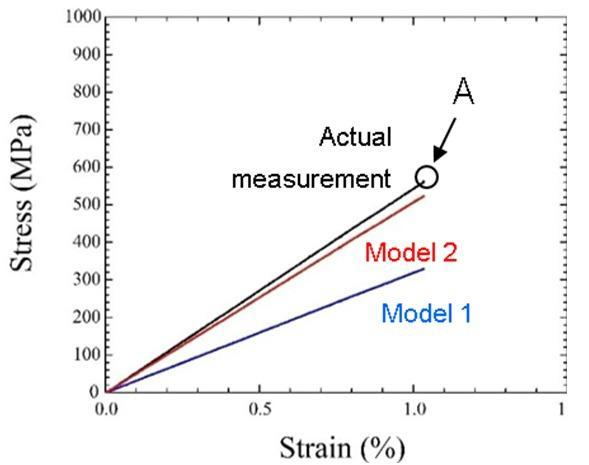
在这种情况下,模型 1 便于进行简单的分析,但不像从 X 射线 CT 成像中获取的模型2可以提供精确的结果。一般来说,研究表明需要进行材料测试验证 CAE 的结果,且 X 射线 CT 对于获取 CFRTP 织物复杂的微观结构形态具有重要意义。
在利用 CAE 分析评估应变分布时,纤维束中纤维的间距与交替的低应变态和高应变态的状态显示定性一致。然而,目前还无法对物理测量和虚拟测试间的应变值进行更精确的定量比较。
结论
本研究采用的分析技术对于通过典型材料的 CFRTP 织物预测复合材料的各向异性行为具有重要的参考价值。对内部结构模型和分析结果的实际测量验证表明,X 射线 CT 有助于提高 CAE/NMT 的准确性,
因此,这些方法能够预测非常复杂的物理现象,如各向异性复合材料中的物理现象,显示出结合实际测量和计算机辅助模拟的重要性。日本计算工程与科学学会进行的高质量计算和标准模拟程序工作正在寻求改进验证的尝试,是更广泛的国际上推动比较真实结果与模拟结果的一部分。采用这种方法,可以有针对性地进行更高效的材料和产品设计。